Standing the Test of Time
Overview
The offshore industry has many over used words and phrases, which often camouflage technical complexity and the criticality of form and function.
Control umbilicals have been required since the first offshore installation and over the years they have become complex and vital engineered components for offshore production.
Ensuring the Reliability and Long Service Life of Subsea Umbilicals
Subsea umbilicals deliver power, communications, hydraulic control and production chemicals to subsea equipment and are an integral element of offshore development. Failure of umbilical components in remote installations can be extremely expensive both in lost production and in rectification. Insufficient knowledge of their complex behaviour has often led to defective design, manufacture, installation and operation.
Umbilical specification is determined by the wide-ranging requirements of diverse disciplines, from reservoir modelling to electrical engineering. These disciplines are well known to the industry but how does an operator maintain the performance of an umbilical to the end of its design life, which is well beyond the manufacturer’s or contractor’s guarantee period? The answer is relatively simple: by identifying the most appropriate design, optimising it and verifying the quality of the materials and production methods. The transportation and installation, which is usually carried out by different teams, are also critical to the operational life of the umbilical. Typically, there are many teams of design engineers, quality experts, and manufacturing specialists from all sides of the contractual relationship, each looking at discreet elements of the journey from data sheet to the finished product. It would be unusual for each individual to be in a position to appreciate fully the effect his or her part in the process will have on the final functional performance of the installed umbilical. So what must an operator actually do to ensure the performance of an umbilical? In short, an independent, technically competent representative for the operator needs to oversee – with executive powers at all stages – the development of the umbilical from initial specification to installation and commissioning. Typically, the resources within an asset-owning or contracting company are not organised to fulfil this function so they have to look to specialised companies to provide this high level engineering capability.
To qualify for this vital service the requirements include the ability to:
- review and contribute to the initial design specification
- technically evaluate the proposals
- carry out a comprehensive design review and optimise the cross section for its service condition
- conduct installation and dynamic analyses
- carry out fatigue life assessments that are based on representative S-N data drawn from fatigue tests for different types of steel tubes, armour wires and conductor cores
- verify the quality plans for the engineering, manufacturing, transportation and installation processes
- verify the quality of the as-built umbilical by mobilising a qualified engineer to the location wherever in the world and be the operator’s executive
- competently sign off the complete process at commissioning.
Typically, umbilicals consist of metallic and non-metallic materials and load bearing armour wires or steel tubes. A principal concern in their evaluation is the analysis of their mechanical behaviour. Tension, torque and bending loads have to be translated into stresses and strains in the constituent components and, more importantly, used to estimate their operational and maximum load capacity. BPP has been involved in two major Joint Industry Projects (JIP) for analysis methodology and have developed a series of software tools for the detailed analysis of complex cross section designs found in the latest designs of umbilicals. As the ever-increasing water depths need to be conquered, these advanced analytical solutions can be used to complement the current industry standard design tools and procedures. The result is to reduce further technical risk and costs by improving the understanding of the mechanics of umbilical cross sections at the design stage. The predictions for stiffness and strength used in such analysis have been validated against empirical tests on a large number of full size specimens.
BPP believe it is also important to appreciate that the analytical approach depends on the type of umbilical. For example, a different set of analytical solutions has to be used for soft-core umbilical structures (those containing thermoplastic hoses and cables) from those used for umbilicals containing steel tubes and other hard material components. The analysis methods behind these BPP software solutions represent the load deformation behaviour of the helical, cylindrical and inner cores of umbilicals as ‘super elements’ with linear elastic material behaviour. A non-linear finite element analysis then uses the super elements to account for the complex contact forces between the layers. A fitness for purpose review or design optimisation process typically starts with an idealised model of the umbilical. An integral component and detailed materials database is used to generate a cross section model that allows the engineer to specify and adjust component type, dimensions, materials and geometry. The software can then be used to translate umbilical tension, torque and bending moments into stresses and strains within the components. This methodology accounts for the structural behaviour of the helical and cylindrical layers as well as the interlayer forces that exist between them. A comprehensive output report is generated which then provides a detailed insight into the mechanical response of the individual components and the structure as a whole. Stiffness and torsional characteristics can be determined with the results being used to calculate the umbilical’s maximum handling tension and strength as well as component stresses and strains for specific handling, installation and operating conditions. This provides not only a complete picture of the umbilical’s mechanical characteristics but also essential input data for comprehensive and thorough dynamic and fatigue life assessments.
It is recognised by operators that whilst the specification and design concept are basic requirements, the quality of execution of the detailed design and manufacture by the umbilical supplier is a critical element to achieving the required design life. However, commercial pressures are at their most intense during this phase, as the manufacturer needs to deliver on time and within budget. At the same time, the operator is tending to increase pressure on the supplier to deliver, as the umbilical installation is a key element of the total project, and any delays could result in lost revenue. It is useful, therefore, to have an independent body that can verify the quality of both the design and manufacture on behalf of the operator, but also to act as an ‘honest broker’ to ensure that the necessary quality is achieved during manufacture.
It is a well-known industry axiom that a ‘good installation is critical to trouble free operation and a long life’. Therefore, it is no surprise that operators will use the expertise of the engineers who oversee the specification, design and manufacture of umbilicals to continue the process for the transportation, installation and commissioning phase. The transportation of the umbilicals is a high risk phase and should be given as much attention as manufacturing.
BPP has the ability to mobilise a highly qualified and experienced team to travel to the umbilical manufacturers at key times where third party 100% surveillance is required during manufacture and initial transportation. BPP can also travel to the operator’s installation base to supervise the offloading and handling of the umbilicals prior to offshore installation. With this level of ‘cradle to grave’ engineering expertise, the goal of achieving a quality installation that will perform reliably during its design life has the highest probability of being attainable.
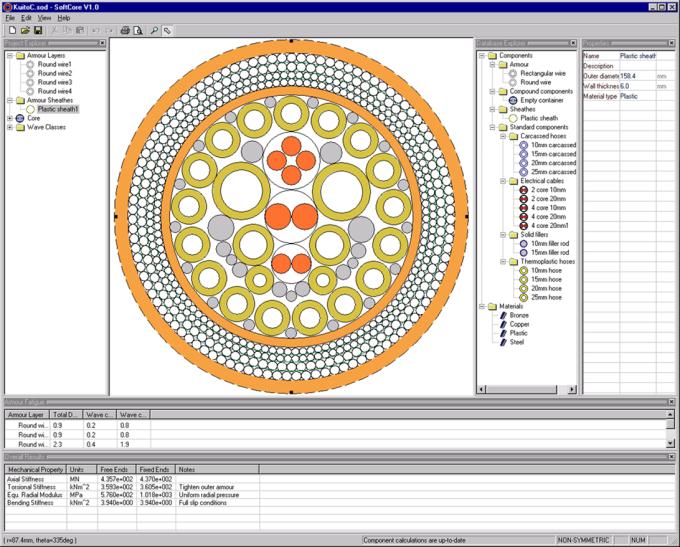
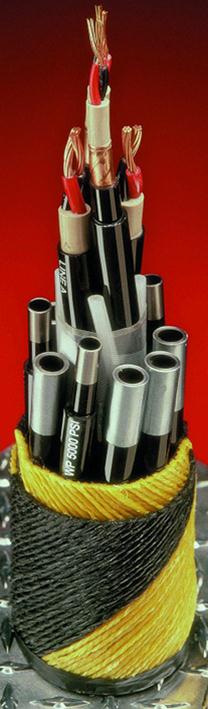
Related Sectors
- Thermal Assessments
- Subsea Cable Engineering
- Subsea Cable Protection
- Electro-magnetic Field Effects
- Cable Condition Investigation
- Telecommunication Cable Services
- Cable Fatigue Life
- Dynamic Cable Ratings
- Cable and Materials Testing
- Cable Manufacturing Support
- ECG™ Holistic Cable Monitoring System
- AI & Machine Learning for Subsea Cable Data